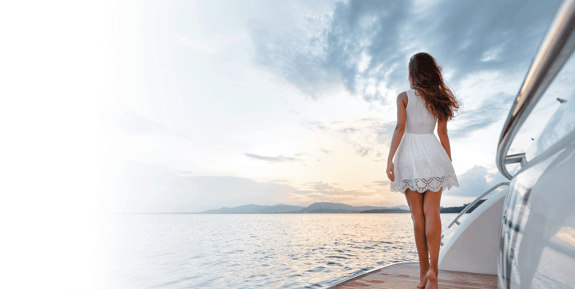
Looking for answers?
LET US HELP
FREQUENTLY ASKED QUESTIONS
When in doubt look for answers here in our FAQ or do not hesitate contacting Smartgyro. For more technical insights, practical guides, and useful articles, be sure to check out our Blog.
Smartgyro stabilizers effectively reduce the boat roll through the force created by the spinning of a flywheel inside a vacuum-enclosed sphere, which is then transferred into the hull structure to counteract wave motion.
If you're eager to dive deep into how gyro stabilizers work and explore the tech details, we've got a special treat for you. Check out our detailed blog post at: blog.smartgyro.com/gyro-stabilization-technology
And if you're not a tech guru but want to explore the science behind gyroscopic stabilizers, we've got you covered. Discover the fundamentals of gyro stabilization technology in an easy-to-understand format at: blog.smartgyro.com/gyro-stabilization-technology-easy
Smartgyro stabilizers are designed to minimize not only boat roll but also downtime during maintenance. Thanks to the unique modular mechanical design, the compact Smartgyro stabilizers can be assembled directly inside the boat and serviced on board, minimizing time spent on maintenance and increasing the installation potential in vessels with small access spaces.
Ideal for both new builds and refit installations, the SG range also features several other innovations that will make you FEEL THE MAGIC:
CONTROL ELECTRONICS
A very efficient control system has been designed. It controls the brake system around the precession axis, by reading sensors placed on the machine, and is capable of monitoring all the boat movements and the flywheel speed and position.
An Inertial Measuring Unit (IMU) is embedded in the control electronics to have a precise real time knowledge of the boat’s behaviour. In this way roll reduction is maximized under every sea condition. Particular care has been put on safety: the electronic module acquires several physical parameters of the machine, like temperature and vibrational status of critical points, warning the operator with specific messages on the operator’s display or directly acting on the machine.
BRAKING SYSTEM
The braking system is a pressurized, closed loop oleo dynamic system, using hydraulic cylinders and proportional valve and acts on the precession axis of the gyroscope in a dynamically and controlled way to maximize roll reduction and efficiency, in every sea condition.
COOLING SYSTEM
Smartgyro gyro stabilizers are liquid cooled to dissipate heat generated by the motor and the spinning bearings. The same circuit, powered by a small, high efficiency brushless pump, is also used for cooling the motor controllers well as the hydraulic manifold. Heat is removed with a heat exchanger and a thermostatic valve, which is connected to an external seawater pump (driven by the control electronics and powered by the boat power supply system).
FLYWHEEL BEARINGS AND VACUUM
The Smartgyro stabilizer uses hybrid ceramic ball bearings to minimize friction during flywheel rotation. To increase overall efficiency, the flywheel rotates in a sealed vacuum, minimizing air drag to increase performance and reduce heat and power consumption. For easy service onboard, the built-in pump automatically restores vacuum after performing maintenance on the sphere. The design of the sphere is cooled with glycol and water, including the motor and bearing pack. The closed inner circuit is filled with cooling liquid (propylene glycol), while the outer circuit provides seawater circulation in the heat exchanger.
DRIVING PERFORMANCE
The Smartgyro automatically locks the gyro’s counteracting forces during high-speed turns to make for smoother sailing.
Whether refitting a classic cruiser or building a modern yacht, Smartgyro’s unique modular construction makes the process seamless. When refitting existing vessels, the Smartgyro base frame can be broken down into parts to allow for installation through narrow access hatches, making the process easier and more cost-efficient.
The gyro stabilizer produces large torques to eliminate boat roll, so it requires supports and structural reinforcements similar to those of the engine. Smartgyro always recommends contacting a shipyard or naval architect who can provide information on the sizing and design of supports.
To learn more, read our dedicated article at blog.smartgyro.com/upgrade-your-boat.
We are confident enough in our design to say that we don’t just make installation possible – we make it easy. Here are the necessary steps to installing a gyro stabilizer during a refit:
1. The right Smartgyro for your boatThe ideal unit for your boat can be determined from basic information such as its length and weight. However, for a more precise calculation, we would recommend contacting our Smartgyro experts, who would be happy to guide you through the process and will provide a roll reduction prediction report based on the vessel's specifications and intended use.
2. Where to install your Smartgyro
Once you've selected your SG unit, you'll need to find its new home. A professional marine engineer can help you to find the ideal spot onboard. The good news is as long as you have enough space behind the midpoint of the boat (aft mid-ship), a Smartgyro can be installed almost anywhere! It can be on or off the centre line, and it can also be above or below the waterline.
3. Consider any modifications
If you are undertaking a refit, chances are you’ll be reviewing the electrical and plumbing systems and updating or removing any obsolete equipment. Next, you'll need to make any necessary modifications to the boat's structure to accommodate the stabilizer and reinforce the hull if necessary. If not already on your “to- do” list, we would recommend a new seacock, for efficient flow of the cooling water.
4. Installing the stabilizer systemThe actual process may vary depending on the stabilizer you choose. In summary, due to the design of our units, as long as there is enough space, installation just requires the gyro to be positioned and fixed to the boat structure. It is a relatively simple process, especially where there is narrow access.
5. Testing, testing, overTo optimize unit performance once the stabilizer is installed, a certified Smartgyro technician can adjust RPM and other parameters. This will ensure the system is fully tested and operational to enable you to enjoy the benefits of stabilization in various conditions.
6. Feel the magic, continue the magic, for years to comeProper maintenance is essential to ensure the long-term performance and reliability of the stabilizer system. Smartgyro modular design is also key to reduce downtime during maintenance. Most gyros must be uninstalled and shipped back to the factory. Other gyro stabilizer manufacturers have adapted their designs, but Smartgyro was always designed to be serviced directly onboard the vessel. This is also the reason why it requires some clearance for maintenance activities and, in exceptional circumstances, a hatch to allow the sphere to be removed.
Both gyros and fins are marine stabilization systems. The clear difference is that the fin stabilizer is installed on the outside of the boat while the gyro stabilizer acts from the inside.
Fin stabilizers are installed on the outside of the boat's hull below the waterline. They can either take advantage of the movement of the water or move on their own to create an opposing force to wave motion.
The Smartgyro gyro stabilizer is a unique individual unit (or sometimes, if needed, multiple units). There are no auxiliary systems that run through the boat, and it can be installed anywhere in the engine room, preferably from the middle of the boat towards the stern. A gyro stabilizer has no protrusions on the hull, which means there are no moving parts in the water. Therefore, compared to fins, gyro stabilizers offer reduced drag and higher hull efficiency, and on most installations, selecting a gyro over fins will result, in addition to other benefits, in higher speed and fuel efficiency.
Smartgyro gyroscopic stabilisers have no impact on the pitching of the boat. Gyro stabilizers are meant to reduce the side-to-side roll that happens naturally to every boat and do not affect the pitching motion.
To increase the gyroscopic force, it is necessary to have a high speed/weight of the flywheel. By eliminating air drag inside the sphere, we can spin our flywheel faster and reduce its weight. Also doing so, the more sensitive components of the unit, such as the bearing pack, are further protected from the harsh salty marine environment.
You may be wondering - WHY DO SOME GYROS NOT HAVE A VACUUM-ENCLOSED SPHERE? Simply because it is more complicated, not only to produce, but also to be maintained. That's why we designed the Smartgyro sphere by filling it with nothing more than air, negating the need for special service tools and allowing the vacuum to be restored automatically with a built-in pump.
Whether you are at anchor or underway, there is no need to turn off your Smartgyro stabilizer. Furthermore, to ensure smoother sailing turns, the Smartgyro stabilizer automatically locks the gyro’s counteracting forces during high-speed turns.
Every gyro stabilizer system, regardless of the brand, can overheat. This is where air-cooling or water-cooling comes into play.
In gyros that do not spin the flywheel in a vacuum, the friction of air generates much of the heat. This is one of the reasons why we chose to spin our flywheel in a vacuum.
We use a mixture of glycol and water. Thanks to the heat exchanger, the mixture is cooled with seawater to dissipate the heat generated by the motor and the bearings inside the sphere. This process also cools the inverter and the hydraulic manifold.
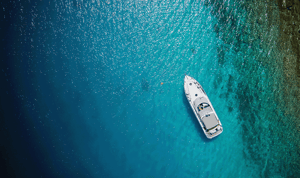
BACKED BY A GLOBAL LEADER
BACKED BY A GLOBAL LEADER
Smartgyro boasts a worldwide distribution network backed by strategic partner YANMAR and its companies, including VETUS, Maxwell, and Flexofold.
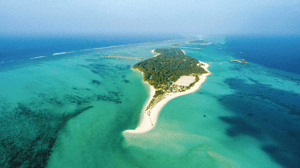
WORLD-CLASS WARRANTY
FROM SMARTGYRO
Smartgyro To Showcase Advanced Stabilization Solutions At Leading European Boat Shows
Start ReadingSmartgyro Returns as Sponsor of the 22nd Carolina Boat Builders Fishing Tournament
Start ReadingSmartgyro Boosts Italian Presence With Appointment of Dealer SV Servizi
Start Reading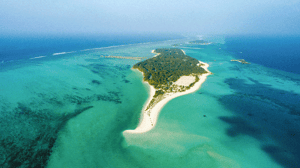